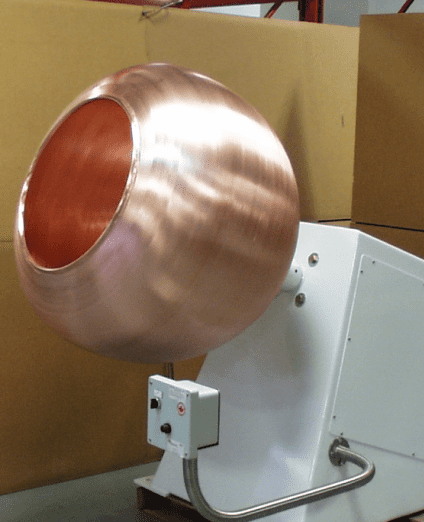
Standard Coating Pan
Standard coating pans are the gold standard for most tablet manufacturers. They are balanced between good efficiency, cost-basis, and a precise, even coating.
All standard coating pans include an air apply, exhaust, pan, liquid, atomizing air, spray nozzle, air suck, and tablet bed.
The circular metal pan can be between 15 to 200 cm (6 to 80 inches) lifted on a benchtop stand and rotated with an electric motor.
Automatic Coating Machine: Each batch of tablets is loaded into the pan before it is set to rotate. Next, a coating solution is sprayed in an atomized form into the pan. The rotating motion allows tablets to tumble and pick up film coating. In addition, an atomized spray provides a more even distribution than using a liquid.
Different machines use different drying techniques. For example, Pellegrino pans, immersion swords, and immersion tube systems differ in the method of drying used.
Our coating pans are made from fully finished stainless steel with an enclosed epoxy powder-coated base. They also have a side panel with a quick access door and front-mounted controls.
Our supporting shaft has two internally mounted bearings for strong support and an external precision shaft seal. The chain-driven coating pan also comes with ultra-clean copper bowls without internal fasteners.
Finally, there are a few options available for our coating pans. You can get apple, onion, or pear-shaped with 38” to 48” diameter. RPMs are added as required, and other customization is possible, including baffles/ribs and the choice between an open or closed base.
Fluidized Bed Coating (Air Suspension System)
The fluidized bed coating system uses a chamber with a vertical cylinder to achieve fluidization. By allowing air to flow from the bottom of the cylinder upward, tablets move up the cylinder and are coated by spray nozzles located at the top and bottom chambers of the system.
The whole system consists of an air atomizing nozzle, atomizing air supply, nozzle liquid feed, exhaust duct, coating chamber, fluidizing air supply, and funnel-like modifier.
By being thrown upwards by air currents in the central cylinder, the nozzles are continuously and evenly coated.
Unfortunately, the system can be rough on the tablets and cause chipping or abrasion. This makes it suitable for only certain drugs.
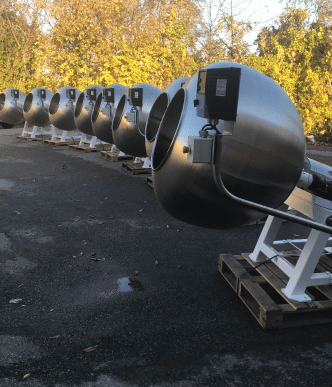
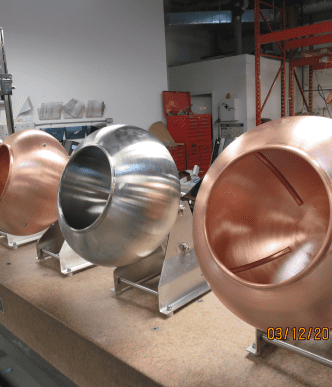
Perforated Pan Coating System
A perforated pan spins on a horizontal axis to coat the tablets evenly. The pan can be either partially or fully perforated.
The parts of this coating system are the inner air supply, exhaust, spray, perforated coating pan, air suck, and tablet bed.
The wholly enclosed system distributes a spray coating composition through a spray bar nozzle or spraying guns positioned at the drum’s center.
For drying, there’s a system that passes directly into the drum with customizable airflow. Its main advantage is a more efficient drying method than the other coating systems.
While their drying systems are often more efficient, the cost and use of perforated pan coating systems can be more difficult.
What is Film Coating on Tablets?
Film coating is the general term for the thin cover applied around a tablet to hide its bad taste. The film coating process does not interfere with the pharmacological components of the drug.
Although the coating of tablets increases both their production and shipping costs, the benefits greatly outweigh the costs.
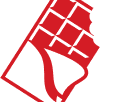
Chocolate and Candy
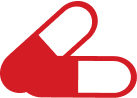
Pharmaceuticals
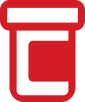
Vitamins and Health Supplements
- The thin layer of coating protects the tongue of the user from bad tastes. This makes it much more likely they’ll be able to take their drugs.
- The coating protects the drugs from moisture and light, which can lower the efficacy of the drugs.
- Drugs can cause irritation and be less effective when released in the esophagus or stomach. The film coating material allows them to release later in the digestive tract.
- The coating also helps with product identity and distinct appearance.
How does the Film Coating System work?
Automatic Control System (PLC)
- This is where you configure the system’s efficiency, consistency, and Touch Screen Operation Panelaccuracy. Most come with inbuilt programmable controls to allow you to choose all your preferred parameters. It will also display the process data, which you can use to record and print the current state of the equipment.
Touch Screen Operation Panel
- This is the human-friendly part of the system interface. It is easy to read the configurations from here.
Electronic Motors
- This is what generates the power used for blowing air or mixing the tablets. Depending on the type of machine, the motors can be used for pumps, exhaust air, hot air, or the drum which distributes the coating. Often, there will be at least three motors in each coating system.
Guide Plate
- This provides help for mixing the tablets safely using the equipment. In addition, it prevents breakage and adhesion of tablets to one another.
Spray System
- This includes the tank, nozzle, and pump. Different parts of the system are used to clean and maintain the spray guns as well.
Peristaltic Pump
- This allows for the thin-film coating to be pumped from the sprayers.
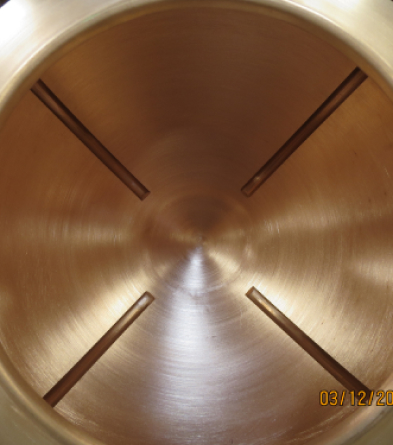
How does a Film-Coating System work?
- First, a polymer is dissolved into a solvent with a few other ingredients to create the film. These include colorant, pigment, opacifiers, and plasticizers.
- You preload your settings to operate the film coating system, then load tablets into the coating drum. The more advanced your equipment, the more automated and efficient it is.
- Usually, operators will check and adjust for uniform coating across the bed. The coating solution is atomized into very fine droplets which are then sprayed into the coating bed as it rotates with the tablets.
- Before the drying air hits the tablets, the solvent binds to the tablet and spreads into a film. Therefore, the overall increase in weight is only 2-3%.
- Depending on the process used, the tablets can be coated more slowly in one batch or more quickly in multiple short-cycle batches. The slow process can cause back-mixing, creating more coatings variation. However, short-cycle mixing is not as efficient of a tablet-coating process.
What are Different Tablet Coatings Made From?
Tablet Coating Machine:
- Sugar coating is one popular choice, called a sucrose solution.
- For their polymer, Meth-acrylic aster copolymer or Ethyl-cellulose are popular choices. These allow you to delay the release of the drugs.
- Solvents are needed to bind the agents and include various chemicals.
- Plasticizers used include polyethylene glycol and propylene glycol.
- Colorants used are mostly standard dyes like FD & C colorant.
Compression coats are also an option for creating a tablet with extended, rapid, or controlled release.
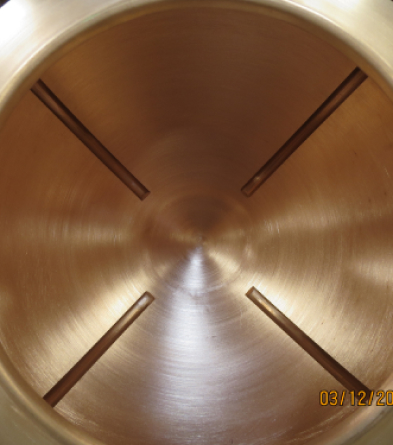