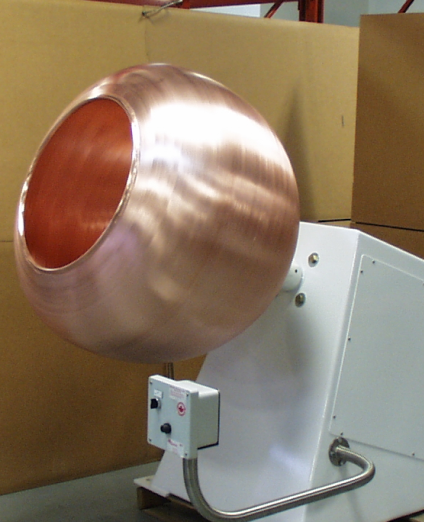
Different types of Coating Machines
Coating machines in pharmaceutical industry used to be big rotating hunks of rollers in which you toss your tablets and roll them in a circular motion as you spray the coating. Not the most uniform coating, but it gets the work done. There have been many technological advancements, and now there are mainly three types of coating methods. Many tablet coating machines are made with advanced modifications to improve their efficiency further.
- Standard Coating
- Perforated Coating
- Fluidized Bed Coating
Each one has a different working principle and different advantages. Different types of tablets will be benefited from different types of coating.
Standard Coating
As the name suggests, standard coating machines coat the tablets with a rotating circular pan 8 to 60 inches attached to an electric motor. Batched tablets are loaded into the pan, where they tumble and get coated with the solution. An inlet with hot air dries the solution down.
There are three variations which are used to increase the efficiency of drying the coating.
● Immersion Sword System in which the hot air is supplied from a perforated tube immersed in the table bed.
● Pellegrini Pan System helps the distribution of hot air using baffles and tapered side walls in the pan.
● The immersion Tube system directly delivers the air in the table bed through a nozzle.
Advantages
- One of the easiest coating methods
- Produces a fairly uniform coating
- Low drying times
Disadvantages
- The risk of uneven coating in the standard method is very high.
Perforated coating
Perforated coaters are made with high capacity in mind. Similar to the standard coating method, there is a rotating drum which rotates with nozzles inside, spraying coating solution at the tablets. As the drums are perforated, the air inlet and suction shoe are outside the drum with spraying guns inside.
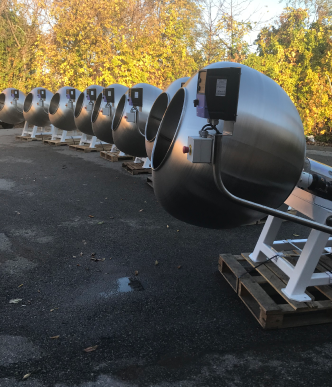
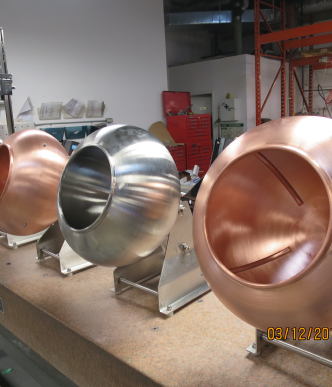
There are four types of perforated coaters:
- Accela-cota is one of the simple implementations with a perforated drum in which hot air is directed from outside and exhausted with the help of a suction shoe.
- Hi-coater systems with similar working as Accela-cota and the nozzle spray downwards, and the air enters the perforated drum from the side and suction shoe at the bottom.
- Driacoaters are systems with drums with perforated ribs protruding inside the drums delivering hot air flow to dry the tablets. The hot air enters the drum from the bottom and flows upwards.
- Glatt coater made for short processing time of the tablets, they are equipped with multiple high-speed nozzles and have high spray rates and fully perforated drums. The drying air is directed from inside and leaves the tablet bed through the suction shoe.
Advantages
- Adequate mixing of the tablets.
- Extremely efficient as drying speed is exponentially increased with perforated drums.
- Production on a large scale can be achieved.
Disadvantages
- The complicated cleaning process needs to be thoroughly cleared after a product changeover.
- Airflow turbulence due to a high air speed quickly dries the coating.
Fluidized bed coating
The fluidised bed, also known as the air suspension system, has a vertical cylinder, and air high-pressure air flows upward, suspending the tables. Then spray nozzles sprays the coating solution. The tables move upwards, outwards and downwards, achieving fluidisation and creating a thing and perfect layer of coating on the tablets.
Different Fluid beds can have nozzles in different positions, and there are generally three types of fluidised beds depending on how they spray the coating solution.
- Top-spray
- Bottom-spray
- Tangential-Spray
Advantages
- High coating efficiency is achieved by the air suspension coater’s capacity to suspend and coat tablets simultaneously.
- It provides a substitute for pan coating and is especially well-liked for multiparticulate systems.
- Produce consistent thin layers from the finely split spray.
Disadvantages
- High maintenance is required for cleaning.
- Electrostatic build-up can occur.
- The fluid bed runs on the principle of fluidisation, which can be ruined with the slightest pressure drop producing non-uniform tablets.
The coating on the tablet can improve the shelf-life, colour, texture and even flavour. Depending on the tablet you produce, you might need a unique solution and coating. Choosing a suitable Tablet machine to coat your tables will help you achieve that.